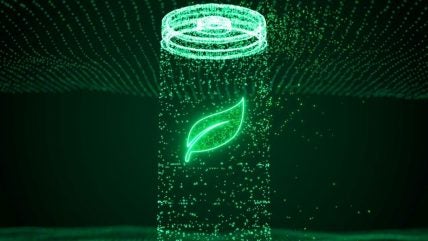
According to thematic research by GlobalData, 2023 saw an increase in awareness of corporate environment, social, and governance (ESG) values compared to previous years, coinciding with a greater discussion of environmental and social issues leading up to the COP28 event in December.
The research also found that pressure from consumers and investors is a key driver behind the creation of ESG strategies, with environmental performance acting as an important deciding factor for many investment companies and buyers. For example, pressure from customers was the primary reason for setting up a plan for 35% of respondents, while pressure from investors was the main driver for 30% of respondents.
For the automotive industry in particular, companies are investing in technologies and practices that promote energy efficiency, such as electric vehicles (EVs), renewable energy, and sustainable supply chains. These initiatives not only help reduce environmental impact but also contribute to cost savings and operational efficiency.
Auto companies are also increasingly focusing on incorporating sustainable materials in their products. In exploring the use of recycled materials, bio-based materials, and a circular economy in auto manufacturing, the recycling of Li-ion batteries has emerged as a viable green solution.
Li-ion batteries are a critical technology in the energy sector and key components of EVs. As a result, a large-scale Li-ion market has emerged, with the battery energy storage market estimated by GlobalData to be worth US$10.84 billion by 2026.
Why should we be recycling batteries?
As the demand for these batteries continues to grow, the need for effective recycling methods becomes crucial to minimise environmental impact and maximise efficiencies. Lithium is a finite resource and must be deployed with care to prevent shortages.
Battery recycling involves the collection, disassembly, and processing of used batteries to recover valuable materials such as lithium, cobalt, nickel, and other metals. Recycling not only helps to conserve limited natural resources but also reduces the environmental footprint associated with the extraction and production of these materials.
Li-ion batteries, for example, contain valuable metals that can be recovered and reused. According to GlobalData research, if battery recycling capabilities are scaled accordingly, by 2040 new mining for battery materials would be almost unnecessary. This would have a significant impact on the availability of mineral resources and overall carbon emissions.
Recycling also helps to prevent pollution by safely managing and treating battery waste. Improper disposal of Li-ion batteries leads to the chemicals and heavy metals present in batteries leaching into soil and water, posing risks to ecosystems and human health.
The recycling of Li-ion batteries in particular requires less energy compared to the production of new batteries from raw materials, and is an essential component of the circular economy, where materials are kept in use for as long as possible. Closing the loop through recycling creates a more sustainable and self-sufficient supply chain for battery materials.
However, challenges still exist in Li-ion battery recycling. The complex chemistry and design of these batteries make the recycling process technically challenging. Additionally, the collection and recycling infrastructure needs to be further developed to handle the increasing volume of used batteries.
How can Frewitt help?
Headquartered in Fribourg, Switzerland, Frewitt is one company making significant advances in the world of battery production. An expert in powder grinding and milling since 1946, Frewitt’s technology has the capacity to mill key components for batteries like graphite and lithium. These materials are especially important in the production of low-carbon EVs.
By equipping its factories with geothermal heat pumps and solar panels, Frewitt expects to become 40% self-sufficient in energy and significantly reduce its carbon emissions. Its commitment to a greener future is further highlighted in its own offering, which has evolved to offer unique battery recycling capabilities.
Increasing the efficiency of solid bulk size reduction of singular battery ingredients, as well as composite materials and eliminating their potential for waste, is a role that Frewitt has taken up for major battery manufacturers and recycling companies.
The complex process of battery recycling
The physical properties of battery ingredients vary dramatically from the dry, dust-generating, and brittle to the moist, spongy, and elastic. These temperature-sensitive products often need to be processed in multiple complex stages. To be capable of recycling materials for reuse in battery components, appropriate conditioning, size reduction, and screening of the materials are critical. All ingredients must be rendered homogeneous in their composition to ensure reuse.
Recyclable battery material is composite material that not only includes the conductive material, but also the metal casing of the housing, cathodes, and anode assemblies, all which must be broken-up, segregated, and screened before downstream processing can begin. Frewitt provides its expertise of combining crushers, lump breakers, and extractors which precondition recyclable material for downstream milling and screening, also carried out by Frewitt. Pre-conditioning can be controlled and metered to ensure optimal screening and milling results, permitting for the material, often known as ‘black mass’, to be rededicated to new battery production.
Depending on the overall size of the material destined for recycling, the volume of the material being recycled, and the physical plant of the customer, Frewitt can scale its equipment to meet the needs of the customer from lab-scale to high volume production levels. Frewitt provides not only turn-key solutions but can also provide critical components for integration in a pre-existing recycling line. Turn-key installations, and other Frewitt components are always manufactured with the finest quality stainless steel. They also offer the option of constant foreign metal object detection, ensuring that quality and conductivity of battery ingredients is preserved.
Sustainability is an evolving concept in the battery industry, but when working with trusted partners like Frewitt, exploring a circular battery economy can be simple and effective.
To find out more about Frewitt’s milling capabilities, download the whitepaper below.